How Screw Air Compressor Works: A Comprehensive Guide to Understanding the Mechanism

Have you ever wondered how air compressors work? Specifically, screw air compressors? Well, wonder no more! In simple terms, screw air compressors use two helical rotors to compress air and generate power. But the real magic happens in the details of how these components work together to produce the desired outcome. Imagine two corkscrews, rotating in opposite directions, one inside the other.
As they turn, they trap air between them and reduce the volume of the air, resulting in compressed air. This process is similar to twisting a towel to squeeze out excess water. Screw air compressors are incredibly efficient and durable, making them the preferred choice for many industrial applications.
They offer several advantages over other types of air compressors, such as reduced noise levels, low maintenance requirements, and sustained, continuous operation. This makes them ideal for industries that rely on compressed air for their operations, such as manufacturing, construction, and energy production. So, if you’re interested in learning more about how screw air compressors work, stay tuned for our upcoming blog posts.
We’ll dive deep into the various components, operating principles, and maintenance requirements of these innovative machines. With our expert guidance, you’ll gain a better understanding of the inner workings of screw air compressors and be well-equipped to make informed decisions related to your industrial operations.
Introduction
If you’re curious about how screw air compressors work, you’ve come to the right place! Unlike traditional reciprocating compressors that use pistons, screw compressors use a rotary screw design to compress air. The screws have a profile that allows them to mesh together and rotate at high speeds, creating an airtight seal that moves the air forwards towards the discharge port. The screws don’t touch each other, which means there is minimal wear and tear, resulting in a longer lifespan and less maintenance.
Screw air compressors are incredibly versatile and can be used in a variety of industries, including manufacturing, construction, and automotive repair. Their efficiency, reliability, and ability to produce compressed air continuously make them an essential piece of equipment in many businesses today.
What is a Screw Air Compressor?
A screw air compressor is a type of air compressor that uses two rotating screws to compress air. It is a popular choice for industrial applications due to its high efficiency and durability. The screws are housed in a chamber and as they rotate, they trap air between them and the chamber walls.
The air is compressed and then pushed out through a discharge valve. The design of a screw air compressor allows for continuous operation without the need for cooling breaks. This type of compressor is commonly used in manufacturing plants, automotive shops, and other industries that require high volumes of compressed air.
If you’re looking for a reliable and efficient air compressor, a screw air compressor may be the right choice for you.
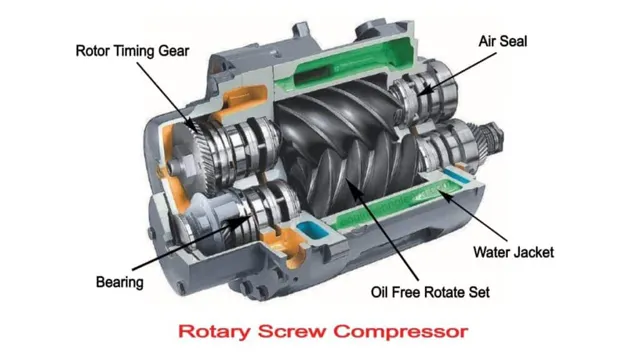
Working Principle
Have you ever wondered how screw air compressors work? Well, it’s actually quite simple. These compressors use two rotating helical screws to compress the air. As the screws turn, the volume between them decreases, causing the air to be compressed.
The compressed air is then released through a valve and stored in a tank for later use. The compression process is continuous, meaning that these compressors can deliver a constant supply of compressed air. Screw air compressors are very efficient and reliable, making them popular in industrial applications.
Whether you need compressed air for a workshop, factory, or other industrial setting, a screw air compressor is a great choice that will provide high-quality results.
Compression Process
When it comes to the compression process, the working principle is based on reducing the size of data files to make them easier to store and transmit. Essentially, this is achieved by removing redundancies in the data. For example, instead of storing every pixel of an image separately, the compression algorithm will look for patterns and similarities among neighboring pixels and store them as a group, resulting in a smaller file size.
The algorithm can also use other techniques, such as replacing repeated words in a text file with a single reference, to further reduce the size of the data. Overall, the goal of compression is to make files more efficient and manageable without sacrificing quality. By using compression, we can store more data on the same amount of storage space, send larger files over the internet, and process data more quickly.
Ultimately, compression plays a vital role in modern technology, allowing us to work with large amounts of data more easily than ever before.
Oil-injected Screw Compressor vs Oil-free Screw Compressor
When it comes to the working principle of oil-injected screw compressors, these machines require oil to lubricate and cool down the internal components. The oil creates a seal between the rotors and the housing, ensuring that the compression process is efficient and effective. As the air enters the compressor, it mixes with the oil, which then absorbs heat from the compression process.
The oil and air are then separated in a separator tank before the clean, compressed air is released. On the other hand, oil-free screw compressors do not require oil as they use special coatings or materials to ensure that the rotors do not touch each other during operation. Instead, these compressors rely on a series of timed and coordinated movements to compress the air.
While oil-free compressors are generally more expensive than oil-injected ones, they do offer certain advantages such as lower maintenance costs, reduced downtime, and lower energy consumption over the long run. Ultimately, the choice between an oil-injected screw compressor and an oil-free one will depend on the specific application and the desired outcomes.
Components of Screw Air Compressors
Screw air compressors are a critical component in many industrial settings, powering tools and machinery across a wide range of applications. These innovative machines use a pair of interlocking screws, or rotors, to compress air as it moves through the system. This process is highly efficient, as it creates a steady, uninterrupted flow of compressed air without the need for pulsation dampeners or surge tanks.
In addition to the rotors themselves, screw air compressors include several other key components that work in tandem to create the desired pressure and flow rate. These include inlet valves, which regulate the inflow of air into the system, and discharge valves, which release compressed air into storage tanks or distribution lines. Some screw air compressors also incorporate cooling systems to prevent overheating, as well as filters and separators to remove moisture and contaminants from the air stream.
The end result is a powerful, reliable source of compressed air that can meet the demands of even the most demanding industrial applications. So, when you’re wondering how screw air compressors work, it all comes down to the careful interplay of these various components, each one contributing to the overall performance and efficiency of the system.
Rotors
Rotors are a key component of screw air compressors, which are widely used in various industrial applications. These devices use two rotors that are closely mounted and rotate in opposite directions to compress air. The rotors have a unique design with lobes that mesh together and form compressed air pockets between them.
This compression mechanism makes screw air compressors highly efficient and enables them to deliver high volumes of compressed air at a consistent pressure. The rotors are typically made from high-quality materials such as cast iron or steel and are precision-engineered to ensure smooth and seamless operation. They are also designed to withstand high temperatures and extreme pressures, making them suitable for demanding industrial applications like manufacturing, construction, and oil and gas exploration.
Importantly, regular maintenance and lubrication are essential for ensuring the long-term performance of the rotors and the compressor as a whole. In summary, rotors are an essential part of screw air compressors and play a crucial role in their function. They are precision-engineered, made from high-quality materials, and designed to withstand extreme conditions.
To ensure their continued performance, regular maintenance and lubrication are crucial. So, if you are looking to invest in a screw air compressor, make sure you choose a reputable supplier with a proven track record of delivering quality products and services.
Cooling System
When it comes to screw air compressors, the cooling system is a crucial component to ensure efficient performance and longevity. The cooling system helps prevent the compressor from overheating and potentially damaging vital parts. One component of the cooling system is the aftercooler, which cools the compressed air before it reaches the next stage of compression.
Another important component is the oil cooler, which maintains a steady temperature of the lubricating oil, preventing it from becoming too hot and reducing its effectiveness. A third component is the water cooler, which cools the water that circulates through the compressor, removing heat generated during operation. It is important to ensure that all of these components are functioning properly to keep the compressor running smoothly.
Regular maintenance and cleaning of the cooling system is also important to prevent clogs and blockages that can hinder performance. By caring for the cooling system, you can ensure that your screw air compressor continues to operate efficiently and effectively for years to come.
Control System
One of the most important components in a screw air compressor is the control system. This system is responsible for regulating the amount of airflow, pressure, and temperature within the compressor, ensuring that it operates efficiently and effectively. There are several key components that make up the control system, including the pressure sensor, temperature sensor, control panel, and motor starter.
The pressure and temperature sensors continuously monitor the compressor’s performance and send data to the control panel, which uses this information to adjust the speed of the motor and the amount of compressed air being produced. The motor starter is responsible for starting and stopping the compressor motor, while also protecting it from overloading or other damage. Overall, the control system plays a critical role in the operation of a screw air compressor, helping to maintain optimal performance and prevent costly downtime.
Advantages of Screw Air Compressors
Screw air compressors are widely used in industrial settings because of their many advantages over other types of air compressors. These compressors are designed to work using two interlocking screws that rotate in opposite directions, creating a seal that compresses the air as it moves through the compressor. This process results in a continuous flow of compressed air, with no pulsations or surges.
One of the biggest advantages of screw air compressors is their efficiency. They are able to produce more compressed air per kilowatt of power compared to other types of compressors. Additionally, they are more reliable and require less routine maintenance.
This reduces downtime and increases productivity. Another advantage is that they are quieter than other types of compressors, making them suitable for use in noise-sensitive environments such as hospitals and schools. Overall, screw air compressors are a great choice for anyone looking for an efficient and reliable way to compress air.
High Efficiency
Screw air compressors are a popular choice in industrial settings for their high efficiency and numerous advantages over other types of compressors. Thanks to their unique design, screw air compressors offer a more consistent flow of compressed air, which means that they can maintain a higher level of efficiency over a longer period of usage. In addition, screw air compressors require less maintenance than other types of compressors, which can save businesses both time and money.
Another advantage of screw air compressors is that they can operate at lower temperatures, which makes them more energy-efficient and therefore better for the environment. Overall, if you’re looking for an efficient and cost-effective option for compressed air, a screw air compressor could be just what you need.
Low Maintenance
When it comes to low maintenance, screw air compressors are hard to beat. These machines are designed to operate with minimal downtime and require little upkeep over their lifetime. Unlike other types of compressors, screw compressors have fewer components and do not require as much lubrication.
This means less time and money spent on maintenance and repairs. Additionally, screw compressors are built with durable materials and can withstand harsh working conditions without showing signs of wear and tear. With their low maintenance requirements, screw air compressors are an ideal choice for businesses looking to reduce their operating costs and improve productivity.
Versatility
Screw air compressors are incredibly versatile machines that have a range of advantages over other types of compressors. One of the biggest advantages is their ability to handle various tasks with ease. These compressors deliver a consistent flow of compressed air that can be used for anything from powering hand tools to driving large machinery.
Screw air compressors are also incredibly efficient, meaning that they can produce the same amount of compressed air as other types of compressors while using less energy. This can save you money on your electricity bill and also reduce your carbon footprint. So if you are looking for a compressor that can handle a variety of tasks and is efficient, a screw air compressor may be the perfect option for you.
Conclusion
In conclusion, the operation of a screw air compressor is like a well-oiled machine โ quite literally. The interlocking screws work together seamlessly to compress air and produce power through a continuous rotary motion. This is no simple twist of fate, but rather a carefully engineered process that maximizes energy efficiency and reduces maintenance costs.
So, the next time you hear the humming of a screw air compressor, remember that it’s not just a noise โ it’s the sound of ingenuity at work!”
FAQs
What is a screw air compressor and how does it work?
A screw air compressor is a type of compressor that uses two rotating helical screws to compress air. These screws rotate in opposite directions, thereby reducing the volume of the air and increasing its pressure.
What are the advantages of using a screw air compressor?
Some advantages of using a screw air compressor include higher efficiency, quieter operation, and more continuous operation compared to other types of compressors. They also provide a higher flow rate and are able to deliver compressed air at a consistent pressure.
Are there any different types of screw air compressors available?
Yes, there are different types of screw air compressors available, such as oil-injected screw compressors and oil-free screw compressors. The main difference between these types is the presence or absence of lubricating oil in the compression chamber.
Can screw air compressors be used for different applications?
Yes, screw air compressors can be used for a wide range of applications, including in manufacturing, construction, automotive, and food and beverage industries. They are also commonly used for air conditioners and refrigeration systems.
How can I maintain my screw air compressor?
Regular maintenance is crucial to ensure the optimal performance and longevity of screw air compressors. Some maintenance tasks include checking and changing the oil, replacing filters, checking for leaks in hoses and connections, and inspecting and cleaning the compressor’s cooling system.
How energy-efficient are screw air compressors compared to other compressors?
Screw air compressors are generally more energy-efficient than other types of compressors due to their rotary design, which results in less energy waste. They also have fewer moving parts, resulting in less friction and lower energy consumption.
What should I consider when choosing a screw air compressor for my business?
When choosing a screw air compressor, it’s important to consider factors such as the required flow rate, the maximum operating pressure, the available power source, and the noise level. It’s also important to choose a trusted and reputable manufacturer and to ensure that the compressor is suitable for the application at hand.