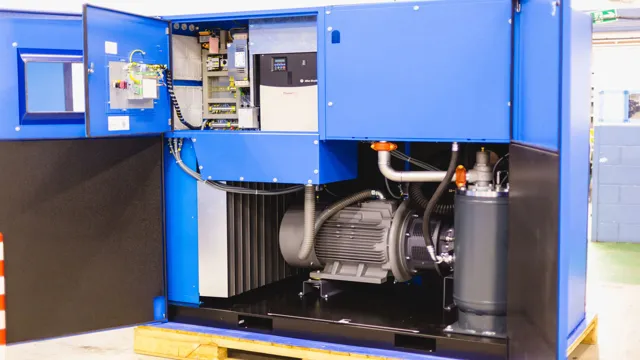
For DIY enthusiasts and professionals alike, having an air compressor is a game-changer for many tasks. But, like any tool, they require regular maintenance, and one of the most important things to know is how to put air in the air compressor. It may sound simple, but there are some steps you need to follow to make sure you do it safely and effectively.
In this blog post, we’ll break down the process step by step and give you tips on how to avoid common mistakes. So, if you’re wondering how to put air in your air compressor, keep reading!
Safety Precautions
Putting air in an air compressor may seem like a straightforward task, but it is important to take safety precautions to avoid potential accidents or injuries. The first step is to read the instruction manual carefully and understand the maximum pressure capacity of your compressor. Make sure to wear appropriate safety gear such as gloves and eye protection before attempting to add air.
Turn off the compressor and bleed any remaining air pressure before opening the tank valve. Slowly add air to the tank while constantly monitoring the pressure gauge and never exceed the maximum pressure limit. Once you have reached the desired pressure, turn off the compressor and close the tank valve before disconnecting the air hose.
Remember to always store your air compressor in a secure and well-ventilated area. By following these safety precautions, you can easily and safely add air to your compressor and keep your equipment in good working condition.
Choose the Right Air Compressor
When it comes to using air compressors, safety should always be a top priority. Before even turning on the compressor, it’s important to ensure all air hoses and tools are properly connected and secured. Loose hoses and fittings can detach and cause serious injury or damage.
Always wear eye and ear protection, as compressed air can be loud and debris can fly up. It’s also important to never exceed the maximum pressure rating of the compressor, as this can cause the tank to burst and potentially cause harm. Regular maintenance and inspection of the compressor can also help prevent accidents, so be sure to follow the manufacturer’s recommendations.
By following these safety precautions, you can avoid accidents and ensure a smooth and successful use of your air compressor.
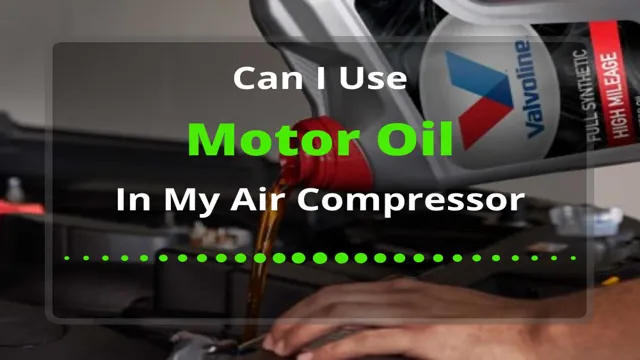
Check the Manual
When it comes to using any equipment, it’s essential to prioritize safety first. One of the simplest yet most crucial steps towards ensuring safety is to read the manual. Often, people may overlook the instructions provided in the user’s manual or assume that they already know how to use the equipment.
However, these manuals contain valuable information that can prevent accidents and injuries. The manual will provide specific instructions on how to handle the equipment, including safety precautions, maintenance instructions, and operational procedures. It’s essential to follow these guidelines precisely to minimize the risk of accidents.
Neglecting the manual may result in injury to the user or damage to the equipment. So, before using any equipment, including the ones you’re familiar with, always read the user’s manual and prioritize safety above everything else.
Steps to Follow
If you’re wondering how to put air in your air compressor, don’t worry – it’s not as complicated as it may seem. The process is fairly simple, and by following a few basic steps, you can have your compressor fully charged and ready to use in no time. First, make sure your compressor is off and unplugged.
Then, locate the air fill valve, which is usually located on the top or side of the compressor. Attach the air hose to the valve, making sure it’s secure. Finally, turn on the compressor and allow it to fill until it reaches the desired pressure level.
It’s important to keep an eye on the pressure gauge while filling, as overfilling can be dangerous. Once you’ve filled the compressor to your desired level, turn it off and unplug it. With these simple steps, you’ll have your air compressor fully charged and ready to use in just a few minutes.
Step 1: Turn off the Compressor
If you’re experiencing issues with your air compressor, the first and most important step is to turn it off immediately. This may seem obvious, but it’s crucial to take this step to prevent further damage or injury. Turning off the compressor stops any air flow and stops the compressor from creating any additional pressure.
This prevents further strain on the compressor and can help prevent any potential malfunctions or damage. Additionally, it’s important to disconnect the power source to ensure that there’s no chance of accidental activation. By taking these first, crucial steps, you can better assess the issue and work towards getting your compressor up and running again.
Remember, safety always comes first.
Step 2: Attach the Hose
Attaching the hose is a crucial step in using a vacuum cleaner effectively. Once you have chosen the appropriate hose for your cleaning requirements, you need to attach it properly to the cleaner and start cleaning your home. First, locate the attachment point for the hose on the cleaner’s body.
It is generally located on the front or side of the cleaner. Then, place one end of the hose firmly over the attachment point and apply pressure until it snaps into place. Make sure it is secured firmly.
Once you have attached the hose, you are ready to use the vacuum cleaner! This simple step will help you clean your room, car or any area with ease, and with the right care, it will give you long-lasting results. Remember to handle the hose with care, so it doesn’t get damaged. So, follow these simple steps and enjoy a clean and tidy space.
Step 3: Open the Valve
Opening the valve is the final step in a complex process of starting up a machine. It is essential to be extra careful while executing this step to prevent damage to the machine or any personnel around it. As you approach the valve, make sure to double-check the pressure gauges and the position of the other switches.
Once you have done that, look for the valve and make sure it is in a closed position. Turn the valve slowly to avoid sudden surges of fluid or gas. Keep a hand near the valve in case you need to turn it off quickly.
Once the valve is partially open, check the pressure gauges again to make sure the flow rate is at the desired level. Open the valve more if needed, being mindful of the pressure and temperature levels. Finally, when the valve is open to the desired level, wait for a few minutes before moving away.
Any sudden changes in pressure or flow rate can cause a burst, so always be cautious. By following these simple steps, you can operate your machine safely and effectively.
Step 4: Monitor Pressure
When it comes to checking the pressure of your tires, monitoring is key. It’s not enough to simply check the pressure once and forget about it. Changes in temperature and overall wear and tear can cause fluctuations in the pressure of your tires, so it’s important to keep an eye on it regularly.
One good rule of thumb is to check your tire pressure at least once a month, or before embarking on a long road trip. Additionally, if you notice any unusual vibrations or handling, it may be a sign of low tire pressure and should be checked immediately. By paying attention to your tire pressure and regularly monitoring it, you can help ensure a safer and more efficient driving experience.
So don’t overlook this important step in tire maintenance!
Troubleshooting Tips
If you’re wondering how to put air in your air compressor, don’t worry, it’s not as difficult as it may seem. The first thing you’ll need to do is check the owner’s manual to find out the recommended air pressure for your specific compressor. Next, ensure that your compressor is turned off and unplugged before attaching the air hose to the valve stem on the compressor tank.
Once the hose is attached, turn on the compressor and let it build pressure until it reaches the recommended level. If you hear any strange noises or notice any leaks, turn off the compressor and immediately inspect for any damage or loose connections. Remember to always use proper safety gear like goggles and gloves when operating any machinery, and never exceed the recommended pressure for your compressor.
With these troubleshooting tips, you can confidently add air to your compressor and complete any job with ease.
Hose Leaks
Hose leaks can be a frustrating issue to deal with, but with a few troubleshooting tips, you can often identify and fix the problem without calling a professional. One common cause of hose leaks is a damaged or worn-out washer. These small rubber or plastic pieces can deteriorate over time, causing water to leak out of the hose connection.
To fix this, simply replace the washer with a new one. Another potential culprit is a loose connection. Check to see if the hose is securely attached to the spigot and other connections.
If not, tighten the connections to stop the leak. Additionally, inspect the hose for any cracks or punctures, as these can also cause leaks. If you notice any damage, replace the hose entirely.
By implementing these troubleshooting tips, you can quickly and easily fix hose leaks and prevent them from becoming a bigger problem.
Burnt Smell
If you’ve ever smelled a burnt odor coming from your appliances, you know how concerning it can be. It’s important to identify the source of the problem immediately, as burnt smells can indicate a fire hazard. The most common cause of a burnt smell from appliances is a build-up of dust or grease on the heating element.
This is particularly common in ovens and stovetops. To troubleshoot this issue, you should turn off the affected appliance and carefully clean the heating element with soap and water. For appliances that are difficult to clean, such as furnaces, it’s best to call in a professional for maintenance.
Other possible causes of a burnt smell include electrical issues, such as faulty wiring, and a malfunctioning motor. In either of these cases, it’s important to cut off power to the affected appliance and seek the assistance of an electrician. Remember, by taking the necessary steps to address burnt smells in your appliances, you can prevent fire hazards and ensure the longevity of your appliances.
Conclusion
Now that you know how to put air in your air compressor, your DIY projects can soar to new heights. Remember, like a balloon, your compressor will only work to its fullest potential if it’s properly inflated. So go ahead and give your tools the power they need, and enjoy the thrill of watching your projects take flight.
Happy compressing!”
FAQs
What is the proper way to check the air pressure in an air compressor?
To check the air pressure, turn off the compressor and unscrew the valve cap on the pressure gauge. Place the gauge onto the valve stem and read the pressure level. If the pressure is too low, use an air compressor to add more air.
Can you use any type of oil in an air compressor?
No, not all oils are suitable for air compressors. It is important to use an oil specifically designed for air compressors to ensure the proper lubrication and longevity of your tool.
How often should you replace the air filter in an air compressor?
It is recommended to replace the air filter every 3-6 months or sooner if it appears dirty. A dirty air filter can cause the compressor to work harder and reduce its lifespan.
What is the difference between a single-stage and two-stage air compressor?
A single-stage compressor compresses air once, while a two-stage compressor compresses air twice. Two-stage compressors are generally more efficient and better for high-demand applications.
What safety measures should you take when working with an air compressor?
Always wear safety glasses and ear protection. Never point the air compressor nozzle at yourself or others. Keep loose clothing, jewelry, and long hair away from the compressor.
How do you drain water from an air compressor tank?
Turn off the compressor and release any remaining pressure. Locate the drain valve at the bottom of the tank and open it to let the water drain out. Be sure to close the valve tightly when finished.
Can you run an air compressor without oil?
No, running an air compressor without oil can cause severe damage to the tool and reduce its lifespan. Always check the oil levels before using the compressor and add more if needed.