
Air compressors are essential tools for a variety of DIY projects and industrial applications. However, purchasing one can be expensive. What if we told you that you could make your own air compressor at home? It’s possible, and not as difficult as you might think.
With a little bit of know-how and some basic materials, you can create a functional air compressor that will serve all your needs. Not only will you save money, but you’ll also gain the satisfaction of creating something with your own two hands. In this blog post, we’ll walk you through the process of making an air compressor at home, step by step.
So, grab your tools and let’s get started!
What You’ll Need
If you’re looking to create an air compressor at home, you’ll need a few key tools and materials. First and foremost, you’ll need a tank to store the compressed air. This can be anything from an old propane tank to a specially-made compressor tank.
Next, you’ll need a compressor pump, which is the heart of the whole system. You can purchase these pumps at hardware stores or online retailers. You’ll also need an electric motor, a pressure switch to control when the compressor turns on and off, and a pressure relief valve to prevent the tank from bursting.
It’s important to note that working with compressed air can be dangerous, so you’ll need to take proper safety precautions and wear protective gear like goggles and earplugs. With these tools and materials, you’ll be well on your way to creating your own air compressor.
1. Motor and Power Source
When it comes to building your own motorized project, there are a few essentials that you’ll need to get started. Firstly, you’ll need a motor. The type of motor you choose will depend on the project you have in mind.
Small DC motors are great for small-scale projects, while larger AC motors may be necessary if you’re working on something bigger. Once you’ve chosen your motor, you’ll need a power source to make it run. This could be anything from batteries to a wall outlet, depending on the kind of motor and project you’re working on.
It’s important to carefully consider the power requirements of your motor to ensure that you choose an appropriate power source. Additionally, you may need other components like wires, switches, and controllers to get your motorized project up and running smoothly. With the right tools and materials, you’ll be able to bring your motorized creations to life and start enjoying the satisfaction of building and creating with your own two hands.
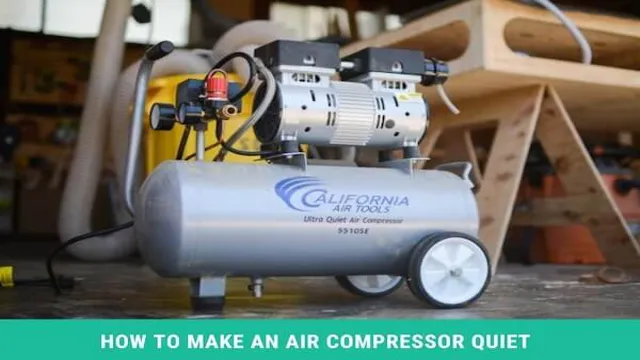
2. Cylinder
When working with cylinder engines, there are a few important tools and pieces of equipment that you’ll need in order to properly maintain and repair them. Firstly, a set of cylinder bore gauges is essential for accurately measuring the diameter of the cylinder bore. You’ll also need a micrometer for measuring the outer diameter of the piston, and a dial indicator for measuring the piston’s depth at various points along the stroke.
Other tools you may need include a cylinder compression tester, a honing machine for removing any imperfections in the bore, and a torque wrench for tightening bolts to the appropriate specifications. Additionally, you’ll need replacement parts such as pistons, piston rings, and cylinder liners. With these tools and parts on hand, you’ll be well-equipped to tackle any cylinder-related repairs or maintenance tasks.
3. Pressure Switch
For those attempting to troubleshoot a malfunctioning HVAC system, it is essential to understand the pressure switch and how it relates to the overall functioning of the equipment. To properly diagnose and repair any issues, you’ll need a few key tools and pieces of equipment. First and foremost, you’ll want a set of gauges to check the refrigerant levels within the unit.
A multimeter is also necessary to check the incoming voltage to the pressure switch, ensuring it is receiving the proper amount of electrical power. Finally, you may need to remove and clean the pressure switch to fix any clogging or blockages within the system. By having these items at hand, you’ll be able to quickly identify any issues causing the malfunction and get your HVAC system running efficiently again.
4. Air Tank
When it comes to setting up a compressed air system, one of the key components that you will need is an air tank. This tank serves as a reservoir that helps to store compressed air that can be used later on. When choosing an air tank, your decision will largely depend on your specific needs and requirements.
The size, shape, and materials used in construction will all play a role in determining which air tank is right for you. In addition, you will want to consider factors such as whether the tank needs to be portable, how it will be mounted, and how much pressure it can safely hold. Overall, selecting the right air tank is an important part of building a reliable and efficient compressed air system.
Step-by-Step Guide
Have you ever thought about making your own air compressor at home? It may seem like a daunting task, but with the right tools and instructions, it can be done easily. Here’s a step-by-step guide on how to make an air compressor at home. First, gather all the necessary materials including a compressor pump, motor, pressure switch, tank, hoses, and fittings.
Next, mount the motor and compressor pump onto the base of the tank. Then, connect the hoses and fittings to the compressor pump and tank, making sure they are tight and secure. After that, attach the pressure switch and wire it to the motor.
Finally, test the compressor and make any necessary adjustments. With this simple guide, you’ll have a homemade air compressor ready to use for all your DIY projects in no time!
1. Mount the Motor and Power Source
When it comes to mounting a motor and power source, it can seem like a daunting task. However, with a little guidance, it can be a simple process. The first step is to gather all the necessary equipment and tools, including the motor, power source, bolts, and nuts.
Next, identify the mounting location for the motor and ensure that it is in a secure position. Then, attach the motor to the mounting location using the bolts and nuts. It is important to tighten the bolts and nuts securely but not too tight to cause damage.
Finally, connect the power source to the motor and test the motor to ensure it is working correctly. Remember, safety should always be a top priority when working with motors and power sources. By following these steps, you can successfully mount a motor and power source and enjoy its benefits in your project or application.
2. Connect the Cylinder
Connecting the cylinder is a crucial step that must be completed correctly to ensure optimal functionality of your machine. First, make sure you have all the necessary tools and accessories for this task. Next, locate the cylinder and inspect it for any visible damages or defects.
Once you have ensured that the cylinder is in good condition, connect the hydraulic hoses to the cylinder. Then, position the cylinder in the correct location and use the bolts to attach it securely. Tighten the bolts evenly to avoid any pressure points.
Once everything is connected, check for any leaks and make sure the cylinder is working correctly. Following these simple steps will help you connect the cylinder successfully and ensure that your machine is functioning correctly. Remember to prioritize safety and accuracy when working with hydraulic systems.
3. Install the Pressure Switch
Installing the pressure switch is a crucial step in most home water systems, and it is not that complicated to do. All you need is a little bit of patience and attention to detail. Here’s a step-by-step guide to help you get started.
Firstly, make sure to turn off the power supply to your water pump before beginning. Then, locate the pressure switch near your water tank and carefully remove its cover. You should see two wire terminals, one for the power supply and the other for the pump.
The wires should already be connected, but if not, connect them now. Next, locate the pressure switch’s adjusting screws and adjust them according to the manufacturer’s instructions until the pressure setting is correct. Finally, replace the cover and turn the power back on to your water pump.
With a properly installed pressure switch, you can enjoy a steady water supply and efficient pump operation.
4. Add the Air Tank
Now that you’ve got all of the necessary components for your air compressor, it’s time to add the air tank. This step is crucial as it will help regulate the pressure of the air as it passes through the system. To begin, make sure your air tank is compatible with the type of air compressor you’re using.
Follow the manufacturer’s instructions for attaching the air tank to the compressor. Most tanks have pre-drilled holes for mounting, so all you need to do is position it in place and secure it with bolts. Make sure all connections are tight and secure before turning on the compressor to test its functionality.
Once you’ve got everything set up, you’ll be ready to start using your newly created air compressor in no time. Remember to check and maintain your system regularly to ensure it’s functioning properly and remains safe to use.
Testing and Safety Precautions
If you’re thinking of making your own air compressor at home, there are some important things to keep in mind. First and foremost, safety should always be your top priority. When working with compressed air, there’s always the risk of the tank or components bursting, which can cause serious injury or even death.
It’s important to follow proper safety precautions, such as wearing protective gear like eye and ear protection, gloves, and a dust mask. Additionally, be sure to test and inspect your equipment thoroughly before use. This includes checking for leaks, verifying proper pressure ratings, and making sure all components are properly installed and tightened.
Remember, taking shortcuts or rushing the process could lead to dangerous situations down the line. With the right precautions and attention to detail, however, making your own air compressor can be a rewarding and enjoyable project.
1. Check for Leaks and Proper Airflow
Checking for leaks and ensuring proper airflow are essential when testing and operating any equipment, especially when dealing with potentially hazardous materials. Leaks can release harmful substances into the environment, leading to serious health and safety risks. Airflow is vital to dissipate heat and prevent overheating, which can cause equipment failure or even fires.
When conducting tests, it is crucial to follow proper safety precautions and use protective gear such as gloves, goggles, and masks. Regular maintenance and inspection of equipment, including hoses, valves, and connectors, can also prevent leaks and ensure proper airflow. By taking the necessary safety measures and conducting routine checks, we can prevent accidents and ensure that our equipment functions safely and efficiently.
2. Follow Safety Guidelines
When it comes to testing and safety precautions, there are a few essential things to keep in mind. First and foremost, it’s crucial to follow any guidelines or instructions provided to ensure safety throughout the testing process. This could include wearing protective gear such as gloves or goggles, testing in a well-ventilated area, and keeping flammable or hazardous materials away from potential sources of ignition.
It’s also crucial to ensure that the equipment and materials you’re using are in good working condition and have been properly stored. Neglecting to follow safety guidelines can not only lead to injury or damage to your equipment but can have serious consequences on your health and well-being. Remember, taking necessary precautions is the first step in successful and safe testing.
Conclusion
In conclusion, making your own air compressor at home is not only a great DIY project, but it also has practical applications for various tasks. With some basic knowledge, a few tools, and some ingenuity, you can create a device that will help you tackle a range of jobs that require compressed air. So whether you’re blowing up balloons or powering pneumatic tools, you can do it all from the comfort of your own home.
Don’t be afraid to get creative and experiment, because the possibilities are endless. Who knows, you might just save a few bucks and impress your friends with your new air compressor creation!”
FAQs
What materials do I need to make an air compressor at home?
To make an air compressor at home, you will need a motor, a compressor pump, an air tank, pressure switch, regulator valve, check valve, and various fittings and hoses.
Can I use an old refrigerator compressor for my homemade air compressor?
Yes, an old refrigerator compressor can be used for a homemade air compressor, but you’ll need to modify it and add a few other components to make it work properly.
How do I assemble the components of my homemade air compressor?
To assemble your homemade air compressor, connect the compressor pump to the motor, then connect the air tank to the pump. Install the pressure switch, regulator valve, and check valve in the appropriate locations, then connect the hoses and fittings as needed.
What kind of motor should I use for my homemade air compressor?
You can use an electric motor or a gas engine for your homemade air compressor, depending on your power source and needs.
How do I maintain my homemade air compressor?
To maintain your homemade air compressor, regularly check and change the oil, clean or replace the air filters, and inspect and tighten all connections and fittings.
What can I use my homemade air compressor for?
You can use your homemade air compressor for a variety of tasks, such as inflating tires, powering air tools, or even painting cars or other objects.
Is it safe to make a homemade air compressor?
As long as you follow proper safety procedures and use quality components, making a homemade air compressor can be safe. However, if you’re not confident in your abilities or knowledge, it may be best to buy a pre-made air compressor instead.