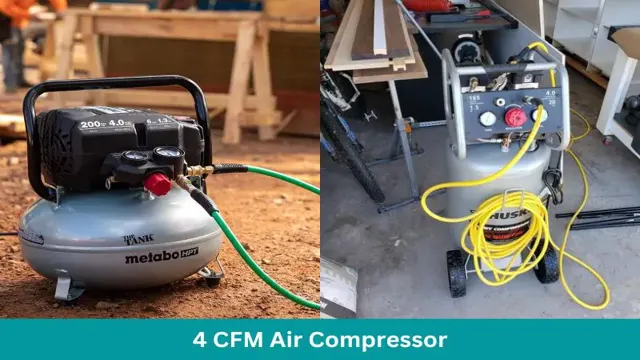
Have you ever wondered how much air your compressor is capable of delivering? Determining the CFM (cubic feet per minute) of an air compressor is crucial for selecting the correct tool for a project. Understanding the CFM of your compressor also helps in maintaining its functionality. However, to determine the CFM, you need to have adequate knowledge of the compressor’s capacity and the tools you will be using.
Think of your air compressor as a car’s engine, and the CFM as its horsepower. Just as an engine’s horsepower determines its capacity and performance, the CFM of an air compressor determines its performance and efficiency. The CFM represents the amount of air that the compressor delivers within a minute.
When using an air-powered tool, it is vital to ensure that the compressor’s CFM output is greater than what the tool requires. If the tool requires more CFM than the compressor is capable of delivering, it will not function appropriately and may lead to damage. Moreover, knowing the CFM of an air compressor is crucial for preventive maintenance and repair.
If there is a drop in the CFM output, it may indicate a mechanical issue that needs to be addressed. By determining the CFM of your air compressor, you can stay alert to potential issues and extend the lifespan of your compressor. In conclusion, understanding the CFM capability of your air compressor is vital for selecting the right tools for a project, maintaining its efficiency, and preventive maintenance.
It’s essential to ensure that the CFM output of your compressor is suitable for the tools you intend to use to ensure optimum performance and avoid damage to both the equipment and the project.
Understanding CFM
If you’re in the market for an air compressor, it’s important to understand what CFM is and how it affects the performance of your compressor. CFM, or cubic feet per minute, is a measurement of the amount of air your compressor can deliver in one minute. The higher the CFM rating, the more air your compressor can deliver, which is important for tasks requiring a lot of air pressure.
To determine the CFM of your air compressor, you’ll need to take into consideration the horsepower of the motor and the size of the tank. Generally speaking, higher horsepower and larger tanks will result in a higher CFM rating. It’s also important to consider the specific task you’ll be using your compressor for, as certain tasks may require a higher CFM rating than others.
So before you buy an air compressor, make sure to research different models and compare their CFM ratings to find the one that’s right for you.
Definition of CFM
Understanding CFM – The measurement of airflow or air volume in cubic feet per minute is called CFM (Cubic Feet per Minute). It is a crucial aspect in air circulation systems for achieving balanced airflows in HVAC systems. It refers to the amount of air a fan can move in one minute.
For instance, if a room has a CFM requirement of 500, that means a fan or air conditioning unit should move 500 cubic feet of air per minute to maintain a comfortable atmosphere. Accurate calculations of CFM play a significant role in the design and installation of HVAC systems. The size of the room, temperature, humidity, and altitude are just a few of the factors to consider when determining the necessary CFM.
Therefore, understanding CFM will go a long way in achieving optimal airflow and efficient HVAC systems while maintaining a comfortable environment.
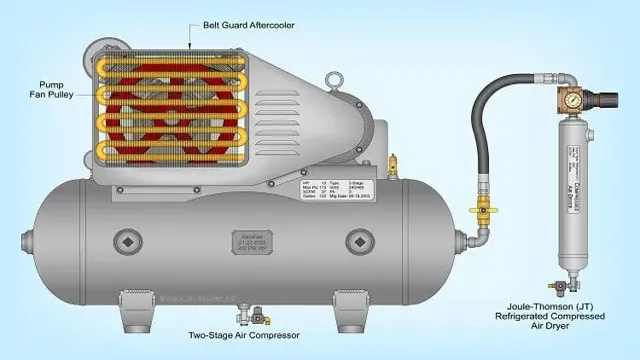
Importance of CFM in Air Compressors
When it comes to air compressors, you may have heard about CFM. But what does it really mean and why is it so important? CFM stands for cubic feet per minute and it is a unit used to measure airflow. In air compressors, CFM represents the amount of air that can be delivered by the compressor per minute.
This is a crucial factor to consider when choosing an air compressor as it determines the compressorโs ability to power tools and machinery. The CFM required will depend on the specific needs of your equipment. If you donโt have enough CFM, your equipment may not function properly, and if you have too much CFM, you may be wasting energy and money.
Itโs important to understand the CFM requirements of your tools and machinery, and to choose an air compressor that delivers the appropriate CFM to prevent any issues.
Factors Influencing CFM
If you’re wondering how to know the CFM of an air compressor, there are a few factors that influence the calculation. First and foremost, the horsepower (HP) of the compressor plays a significant role in determining the CFM output. Generally, the higher the horsepower, the more CFM the compressor will produce.
However, it’s worth noting that the efficiency of the compressor motor can also impact the CFM. Other important factors to consider are the tank size and pressure rating. A larger tank size will typically result in more CFM output, while a higher pressure rating can increase the efficiency of the compressor.
Additionally, the type of compressor (e.g. single-stage, two-stage) and the design of the compressor’s pistons and valves can influence the CFM.
By taking these factors into account, you can get a better idea of how to calculate the CFM of your air compressor. And remember, if you’re unsure, it’s always best to consult the manufacturer’s specifications or seek guidance from a professional.
Horsepower of the Air Compressor
When it comes to air compressors, horsepower plays a big role in determining the unit’s performance. However, it’s not the only factor that determines how much air the unit can deliver. Cubic Feet per Minute (CFM) is another crucial factor that affects an air compressor’s efficiency.
CFM measures the amount of air that a compressor can move in a minute. While a higher horsepower rating typically indicates a higher CFM, there are other factors that influence CFM, such as the cylinder size, pump efficiency, and tank size. The bigger the cylinder and the more efficient the pump, the higher the CFM.
Additionally, air tanks that are too small or don’t have enough pressure can hinder the compressor’s CFM output. It’s important to consider all these factors when selecting an air compressor to ensure that it can deliver the required amount of air for your specific needs, whether for industrial or DIY applications.
Size of the Air Tank
When it comes to air compressors, one of the factors that can greatly affect CFM (cubic feet per minute) is the size of the air tank. A larger air tank means that there is more compressed air available, which can result in higher CFM. This is because the compressor can build up more pressure before it needs to turn on and start compressing more air.
However, it’s important to note that a larger tank also means a heavier, bulkier compressor, which may not be practical for certain applications. Additionally, there are other factors that can influence CFM, such as the horsepower of the compressor’s motor, the compressor’s efficiency, and the accessories being used with the compressor. Ultimately, it’s important to consider all of these factors when choosing the right air compressor for your needs, rather than solely focusing on the size of the tank.
Maximum Pressure Rating
When it comes to air compressors, understanding the maximum pressure rating is crucial to ensuring optimal performance and longevity. The maximum pressure rating refers to the highest amount of pressure the compressor can produce without risking damage to the unit or any connected equipment. However, several factors influence the compressor’s ability to deliver the required CFM (cubic feet per minute) at a given pressure level.
These factors include the compressor’s horsepower, tank size, and the length and diameter of the air hoses. A smaller tank or a longer hose can reduce the compressor’s ability to maintain consistent CFM at higher pressures. On the other hand, a larger tank and shorter air hoses can help maintain consistent CFM levels and maximize the compressor’s performance.
Ultimately, to achieve optimal results and avoid potential damage, it’s essential to consider these factors and choose a compressor with a maximum pressure rating that aligns with your specific needs.
Ambient Temperature and Pressure
When it comes to determining CFM (cubic feet per minute), there are a few factors that come into play. One of the most important factors is ambient temperature and pressure. This refers to the temperature and air pressure that surrounds the system in question.
As the temperature increases, the density of the air decreases which in turn, affects the performance of the system. This is because the system is designed to operate under specific conditions, and when these conditions change, the CFM will be affected. Additionally, changes in air pressure can also impact the CFM.
As the pressure decreases, the air becomes less dense, which can also affect the system’s performance. So when determining CFM, it’s important to take into account both the temperature and pressure of the surrounding environment.
Calculating CFM
If you’re wondering how to know CFM of air compressor, it’s essential to understand what CFM means first. CFM stands for cubic feet per minute, which is a measurement of a compressor’s airflow rate. To calculate CFM, you need to consider both the compressor’s displacement and how often it cycles per minute.
You can calculate the displacement by multiplying the bore, stroke, and number of cylinders. Once you have that figure, you need to multiply it by the total number of cycles per minute, which is usually the RPM divided by two, before dividing it by 1728 (the number of cubic inches in a cubic foot). This will give you the CFM rating.
Keep in mind that this is an estimated value as CFM can be affected by factors like temperature, pressure, and humidity. Understanding the CFM rating is essential when choosing the right compressor for your specific needs and will ensure you get the most efficient and effective tool for the job.
Step-by-Step Guide on Calculating CFM
Calculating CFM can seem like a daunting task, but with the right tools and knowledge, it can be easily accomplished. CFM, or cubic feet per minute, is a measurement of airflow used in HVAC systems and other industries. To calculate CFM, you need to know the area of the space you want to cool or heat and the desired air changes per hour (ACH).
Multiply the area by the ACH to determine the total air volume of the space. Then, divide this number by 60 to get the CFM. Another important factor to consider is the air velocity in feet per minute (FPM).
This can be calculated by dividing the CFM by the area of the duct or opening. By knowing how to calculate CFM and considering air velocity, you can ensure that your HVAC system is properly sized and operates efficiently.
Conclusion
In conclusion, determining the CFM of an air compressor may seem like a daunting task, but with a little bit of know-how and patience, you can easily become an air compressor CFM sleuth. Whether you’re a DIY enthusiast or a seasoned professional, understanding the CFM of your air compressor is essential for ensuring that your tools and equipment perform at their best. So, don’t be a CFM rookie any longer.
Get out there and start measuring your air compressor’s CFM like a boss!”
FAQs
What is CFM in air compressors?
CFM stands for cubic feet per minute and is a measure of the volume of air flow that an air compressor can provide.
How is CFM calculated in an air compressor?
CFM is calculated by measuring the amount of air that is delivered per minute by the compressor pump, at a specific PSI.
What is the importance of CFM in air compressors?
CFM plays a crucial role in determining the overall performance of an air compressor. It affects the speed and power of pneumatic tools and also determines the maximum pressure that the compressor can produce.
How to choose an air compressor based on CFM requirements?
To choose an air compressor based on CFM requirements, you should first determine the minimum CFM required for your tools or applications. Then, you can select an air compressor that provides the required CFM with some extra margin for better performance.
Can CFM be improved in an air compressor?
Yes, CFM can be improved in an air compressor by increasing the size of compressor pump or tank, improving the air intake system, or reducing the pressure drop in the air lines.
What are some common factors that affect CFM in air compressors?
Some common factors that affect CFM in air compressors are compressor pump size, tank size, motor horsepower, regulator settings, air line length and diameter, and ambient temperature and humidity.
How can low CFM affect the operation of air tools?
Low CFM can cause air tools to operate slower, weaker, or less efficiently than intended. It can also cause the compressor to run more often, overheat, or wear out faster due to increased load and stress.