
Have you ever found yourself in need of compressed air, only to realize you don’t have an air compressor? Fear not, because building your own homemade air compressor is easier than you might think. Not only will you save money, but you’ll also have the satisfaction of knowing that you built it with your own two hands. With just a few tools and some basic knowledge, you can build your very own air compressor that will serve all your compressed air needs.
From filling up tires to powering pneumatic tools, a homemade air compressor is a valuable addition to any DIYer’s toolkit. In this blog, we’ll walk you through the steps to build a homemade air compressor from scratch, including the materials and tools you’ll need, safety considerations, and detailed instructions on how to assemble it all. We’ll also cover some tips and tricks to ensure your compressor works efficiently and effectively.
Whether you’re a seasoned DIYer or just starting out, building an air compressor is a great project to take on. So grab your safety goggles and let’s get to work!
Introduction
Have you ever needed to inflate a tire or power a pneumatic tool, but didn’t want to shell out big bucks for a store-bought air compressor? Fear not, as you can easily build your own homemade air compressor with just a few simple tools and some basic knowledge of how compressors work. The process involves creating a compressor pump from an electric motor, a length of metal pipe, and a few round plates to create a cylinder head. Once the pump is assembled, it can be attached to a tank that you can either buy or make yourself.
Add in some pressure gauges, safety valves, and a regulator, and you’ve got yourself a fully functioning air compressor that you can customize to fit your needs. With this homemade air compressor, you’ll be able to save money and have the satisfaction of knowing you built something yourself. So why not give it a try and see what you can create?
Understanding the basics of air compressors
Air compressors are a vital piece of machinery used in a variety of industries to compress air and then release it to perform different tasks. Essentially, they function by converting electrical energy into kinetic energy that helps compress and store air in a holding tank. Once the air is stored, it is released via a regulator, which can be adjusted to change the output pressure according to the task at hand.
Air compressors come in a variety of sizes and styles and are used for diverse tasks ranging from inflating balloons to powering industrial tools. So, whether you are a DIY enthusiast or a professional contractor, understanding the basics of air compressors is critical to making informed decisions when it comes to purchasing one that fits your needs.
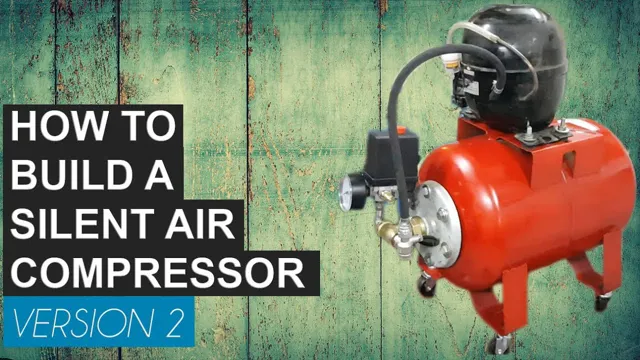
Gathering the required materials
When it comes to crafting a new DIY project, the first step is always gathering the required materials. Depending on the project, this can range from simple tools like a hammer and screwdriver to more specific materials like wood or fabric. Before getting started, it’s important to create a list of all the necessary items so you don’t find yourself halfway through the project without something crucial.
Take the time to research the best materials for your project and make sure you have all the right tools on hand. By doing so, you’ll be setting yourself up for success and ensuring that your finished project turns out just as you envisioned. So, grab a notepad and pen and start brainstorming everything you’ll need to make your DIY dreams a reality!
Building the compressor
Building a homemade air compressor can be a fun and satisfying DIY project. To start, gather the necessary materials including an air tank, an electric motor, and a compressor pump. Begin by mounting the motor onto a sturdy base and attaching the compressor pump to the motor shaft.
Then, attach the air tank to the compressor pump using a pressure switch and pressure gauge. It’s important to note that safety precautions such as wearing protective gear and taking proper electrical precautions should be taken when building your own air compressor. Once everything is securely fastened and wired properly, you can test your creation by plugging it in and filling the air tank with compressed air.
With a little patience and attention to detail, you can have a fully functioning and cost-effective air compressor ready to use for all your DIY projects.
Assembling the tank and pump
Assembling the tank and pump can be a daunting task, but with the right instructions, it’s a breeze to build a high-quality compressor. One of the most crucial parts of the compressor is, of course, the pump. So, it’s essential to choose a pump that suits the specific needs of your project.
Once you’ve made that decision, the next step is to attach the pump to the tank. To do this, you’ll need to use a mounting plate or bracket. Once the pump is secured in place, it’s time to install the tubing and connectors needed to get the air flowing from the tank to your tools.
Depending on the model of the compressor, this may involve using a regulator to adjust the pressure in the tank. With the connections in place, you can then plug in the compressor and start testing it out. With the right setup, you’ll be able to achieve maximum efficiency and get the job done more quickly.
Connecting the motor and pressure switch
When building a compressor, one of the crucial steps is connecting the motor and pressure switch. It’s essential to ensure the connections are made correctly, or else the motor can’t start, or the pressure switch may not work correctly. To start, identify the appropriate wires from the motor and pressure switch.
Run these wires through the conduit, ensuring they stay clear of any moving parts. Once you’ve run the wires through the conduit, connect the wires to the terminals on the pressure switch. The exact location of the terminals may vary depending on the type of pressure switch being used.
Make sure the connections are tight and secure, using a wire nut if necessary. Next, connect the other end of the wire to the motor. Check the motor wiring diagram to ensure the correct connections are made, as connecting the wrong wires can damage the motor or even cause it to fail.
Once all the wiring is connected, you’re ready to turn on the compressor and test it to ensure that everything is running smoothly. Following these steps will ensure your compressor runs smoothly and efficiently.
Installing the control valve and regulator
When building a compressor, one of the essential components is the control valve and regulator. These components help control the flow and pressure of the compressed air. Installing them correctly is critical for the compressor’s overall performance.
One important thing to remember is to follow the manufacturer’s instructions and specifications. It’s also crucial to ensure that the control valve and regulator match the compressor’s size and capacity. Proper installation may involve using wrenches, thread sealant, and Teflon tape.
Once the control valve and regulator are securely installed, it’s advisable to test the compressor’s performance before using it on a larger scale. A well-functioning compressor not only ensures efficient operations but also increases productivity. By giving proper attention to details during installation, the compressor will provide reliable service for an extended period.
Testing and troubleshooting
If you’re thinking about building a homemade air compressor, there are a few important considerations to keep in mind throughout the process. First and foremost, safety should always be your top priority. Make sure you carefully follow all instructions and use appropriate protective gear, especially when dealing with high-pressure components.
Another key factor is testing and troubleshooting. Once you’ve assembled your compressor, it’s essential to carefully check everything for leaks, damage, and other potential issues. This includes testing the pressure switch, relief valve, and any other mechanical or electrical components.
If you do encounter any problems, don’t panic – instead, take a systematic approach to troubleshooting, checking each component one at a time until you identify the source of the issue. With a little patience and some basic troubleshooting know-how, you can build a safe, effective homemade air compressor that will serve you well for years to come.
Checking for leaks
When it comes to checking for leaks in your home, it’s important to take a systematic approach in testing and troubleshooting. First, make sure to turn off all water sources and check the water meter for any movement. If the meter does move, it means there is still water running somewhere, and you’ll need to investigate where.
One simple test is to add a few drops of food dye to the toilet tank and see if it appears in the bowl within 15 minutes without flushing. If so, you likely have a leaky flapper and will need to replace it. Another way to test for leaks is to shut off all water sources and listen for any unusual sounds- like running water- coming from your pipes or fixtures.
If you’re still having difficulty locating the source of the leak, it may be wise to call in a professional plumber to assist with troubleshooting and repairs. Remember, regular leak tests can help prevent costly water damage and keep your home running smoothly.
Testing the pressure and airflow
When dealing with HVAC systems, testing the pressure and airflow is crucial to ensure proper functionality. Testing the pressure involves measuring the static pressure and the pressure drop across the system. Static pressure refers to the resistance of the system to airflow when the system is not in use, while pressure drop is the difference in pressure between the system’s input and output.
A high static pressure can indicate dirty filters or blocked ducts, and a high pressure drop can indicate a clogged coil or other issues. Testing the airflow involves measuring the volume of air being moved by the system. A low airflow can indicate issues like a blocked or dirty air filter, undersized ducts, or a malfunctioning blower motor.
Troubleshooting these issues can involve changing filters, cleaning ducts and coils, or repairing or replacing faulty components. By properly testing and troubleshooting pressure and airflow issues, HVAC systems can operate efficiently and effectively, keeping homes and businesses comfortable year-round.
Conclusion
Congratulations! You now have the power to compress air like a pro. Whether you need it for inflating tires, powering tools, or just impressing your friends, your homemade air compressor is sure to do the job. And who knows, maybe someday you’ll even start your own DIY garage and become the next Tim “The Toolman” Taylor.
But for now, sit back, relax, and enjoy the sweet sound of compressed air. Just don’t forget to wear ear protection!”
FAQs
What materials are needed to build a homemade air compressor?
The materials needed to build a homemade air compressor include an air tank, pressure switch, electric motor, piping and fittings, and various tools.
What is the maximum pressure that a homemade air compressor can reach?
The maximum pressure that a homemade air compressor can reach depends on the capacity of the air tank and the specifications of the pressure switch. Typically, homemade air compressors can reach pressures of up to 150 PSI.
Can a homemade air compressor be used for painting?
Yes, a properly built homemade air compressor can be used for painting. However, it is important to ensure that the air compressor produces clean, dry air to avoid any unwanted particles or moisture in the paint.
Is it cheaper to build a homemade air compressor or buy one?
Building a homemade air compressor can be cheaper than buying a new one, especially if you have access to some of the required materials and tools. However, it also requires significant time and effort to assemble the components correctly.
How long does it take to build a homemade air compressor?
The time required to build a homemade air compressor will vary depending on the complexity of the design and the builder’s skill level. It could take anywhere from a few hours to several days or weeks to complete.
Can a homemade air compressor be used for high-powered pneumatic tools?
Yes, a properly built homemade air compressor can be used to power high-powered pneumatic tools such as impact wrenches, air drills, and grinders. However, it is important to ensure that the air compressor is capable of producing enough air flow and pressure to operate these tools.
How often does a homemade air compressor need to be serviced?
Homemade air compressors should be serviced regularly, ideally every 6-12 months, to ensure that they are functioning properly and to identify any potential issues before they lead to equipment failure. This may include inspecting and replacing worn-out components or lubricating moving parts.
